The lithium battery pack module is mainly composed of batteries and freely combined cooling and heat dissipation monomers. The relationship between the two complements each other. The battery is responsible for powering the new energy vehicle, and the cooling unit can handle the heat generated by the battery during operation. Different heat dissipation methods have different heat dissipation media.
If the temperature around the battery is too high, these materials will use the heat-conducting silicone gasket as the transmission path, smoothly enter the cooling pipe, and then absorb heat through direct or indirect contact with the single battery. The main advantage of this method is that it has a large contact area with the battery cells and can absorb heat evenly.
The air cooling method is also a common method of cooling the battery.(PTC Air Heater) As the name suggests, this method uses air as the cooling medium. Designers of new energy vehicles will install cooling fans next to the battery modules. In order to increase the air flow, vents are also added next to the battery modules. Affected by air convection, the lithium battery of a new energy vehicle can dissipate heat quickly and maintain a stable temperature. The advantage of this method is that it is flexible, and it can dissipate heat by natural convection or by forced heat dissipation. But if the battery capacity is too high, the effect of air cooling heat dissipation method is not good.
The box-type ventilation cooling is a further improvement of the air cooling and heat dissipation method. In addition to controlling the maximum temperature of the battery pack, it can also control the minimum temperature of the battery pack, ensuring the normal operation of the battery to a large extent. However, this method leads to a lack of temperature uniformity in the battery pack, making it prone to uneven heat dissipation. The box-type ventilation cooling strengthens the wind speed of the air inlet, coordinates the maximum temperature of the battery pack, and controls the huge temperature difference. However, due to the small gap of the upper battery at the air inlet, the gas flow obtained does not meet the heat dissipation requirements, and the overall flow rate is too slow. If things go on like this, the heat accumulated on the upper part of the battery at the air inlet is difficult to dissipate. Even if the top is slit in the later stage, the temperature difference between the battery packs still exceeds the preset range.
The phase change material cooling method has the highest technological content, because the phase change material can absorb a large amount of heat according to the temperature change of the battery. The great advantage of this method is that it consumes less energy and can reasonably control the temperature of the battery. Compared with the liquid cooling method, the phase change material is not corrosive, which reduces the pollution of the medium to the battery. However, not all new energy trams can use phase change materials as cooling medium, after all, the manufacturing cost of such materials is high.
As far as the application is concerned, fin convection cooling can control the maximum temperature and maximum temperature difference of the battery pack within the range of 45°C and 5°C. However, if the wind speed around the battery pack reaches a preset value, the cooling effect of the fins through the wind speed is not strong, so that the temperature difference of the battery pack changes little.
Heat pipe cooling is a newly developed heat dissipation method, which has not yet been officially put into use. This method is to install the working medium in the heat pipe, once the temperature of the battery rises, it can take away the heat through the medium in the pipe.
It can be seen that most heat dissipation methods have certain limitations. If researchers want to do a good job in the heat dissipation of lithium batteries, they must set up heat dissipation devices in a targeted manner according to the actual situation, so as to maximize the heat dissipation effect. , to ensure that the lithium battery can work normally.
✦The solution to the failure of the cooling system of new energy vehicles
First of all, the service life and performance of new energy vehicles are directly proportional to the service life and performance of lithium batteries. Researchers can do a good job in thermal management according to the characteristics of lithium batteries. Because the heat dissipation systems used by new energy vehicles of different brands and models are quite different, when optimizing the thermal management system, researchers must choose a reasonable heat dissipation method according to their performance characteristics in order to maximize the heat dissipation system of new energy vehicles effect. For example, when using a liquid cooling method(PTC Coolant Heater), researchers can use ethylene glycol as the main heat dissipation medium. However, in order to eliminate the disadvantages of liquid cooling and heat dissipation methods, and prevent ethylene glycol from leaking and polluting the battery, researchers need to use non-corrodible shell materials as the protective material for lithium batteries. In addition, researchers must also do a good job of sealing to minimize the probability of ethylene glycol leakage.
Secondly, the cruising range of new energy vehicles is increasing, the capacity and power of lithium batteries have been greatly improved, and more and more heat is generated. If you continue to use the traditional heat dissipation method, the heat dissipation effect will be greatly reduced. Therefore, researchers must keep pace with the times, constantly develop new technologies, and select new materials to improve the performance of the cooling system. In addition, researchers can combine a variety of heat dissipation methods to expand the advantages of the heat dissipation system, so that the temperature around the lithium battery can be controlled within an appropriate range, which can provide inexhaustible power for new energy vehicles. For example, researchers can combine air cooling and heat dissipation methods on the basis of selecting liquid heat dissipation methods. In this way, the two or three methods can make up for each other's shortcomings and effectively improve the heat dissipation performance of new energy vehicles.
Finally, the driver must do a good job in the daily maintenance of new energy vehicles when driving the vehicle. Before driving, it is necessary to check the running status of the vehicle and whether there are safety faults. This review method can reduce the risk of traffic failure and ensure driving safety. After driving for a long time, the driver should regularly send the vehicle for inspection to check whether there are potential problems in the electric drive control system and heat dissipation system in time to avoid safety accidents during the driving of new energy vehicles. In addition, before purchasing a new energy vehicle, the driver must do a good job of investigation to understand the structure of the lithium battery drive system and heat dissipation system of the new energy vehicle, and try to choose a vehicle with a good heat dissipation system. Because this type of vehicle has a long service life and superior vehicle performance. At the same time, drivers should also understand certain maintenance knowledge in order to deal with sudden system failures and reduce losses in time.

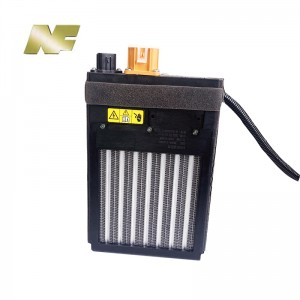
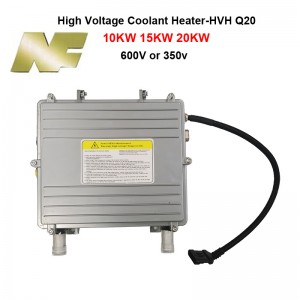
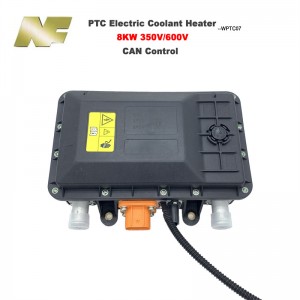
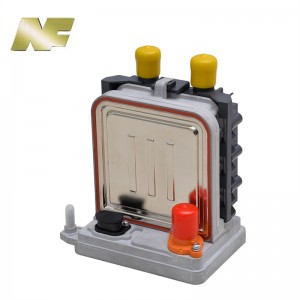
Post time: Jun-25-2023