The thermal management system of a car is an important system for regulating the environment of the car cabin and the working environment of the car parts, and it improves the efficiency of energy use through cooling, heating and internal conduction of heat. Simply put, it is like people need to use fever relief patch when they have a fever; and when the cold is unbearable, they need to use baby warmer. The complex structure of pure electric vehicles cannot be intervened by human operation, so their own "immune system" will play a vital role.
The thermal management system of pure electric vehicles assists in driving by maximizing the use of battery energy. By carefully reusing the heat energy in the vehicle for air conditioning and batteries inside the vehicle, thermal management can save battery energy to extend the driving range of the vehicle, and its advantages are especially significant in extreme hot and cold temperatures. The thermal management system of pure electric vehicles mainly includes the main components such as high-voltage battery management system (BMS), battery cooling plate, battery cooler, high-voltage PTC electric heater and heat pump system according to different models.
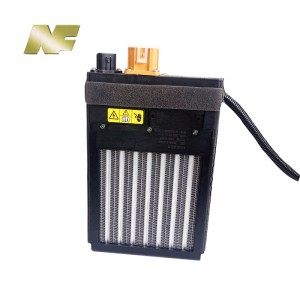
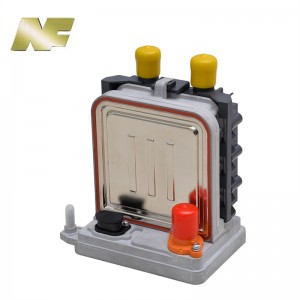
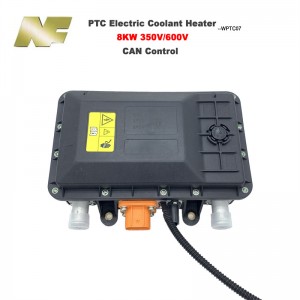
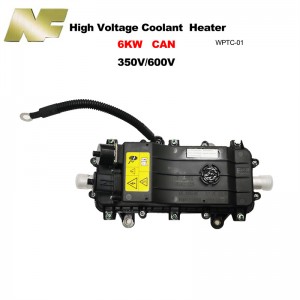
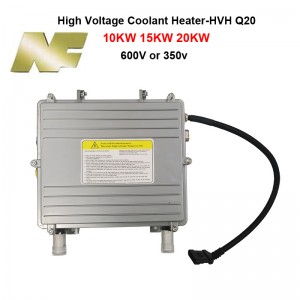
Battery cooling panels can be used for direct cooling of pure electric vehicle battery packs, which can be divided into direct cooling (refrigerant cooling) and indirect cooling (water-cooled cooling). It can be designed and matched according to the battery to achieve efficient battery operation and extended life. The dual circuit battery cooler with dual media refrigerant and coolant inside the cavity is suitable for the cooling of pure electric vehicle battery packs, which can maintain the battery temperature in the high efficiency area and ensure the optimal battery life.
Pure electric vehicles do not have a heat source, so a high voltage PTC heater with a standard output of 4-5kW is required to provide fast and sufficient heat to the interior of the vehicle. The residual heat of a pure electric vehicle is not sufficient to fully heat the cabin, so a heat pump system is required.
You may be curious as to why hybrids also emphasize a micro-hybrid, the reason for the division into micro-hybrids here is: hybrids that use high-voltage motors and high-voltage batteries are closer to plug-in hybrids in terms of thermal management system, so the thermal management architecture of such models will be introduced in the plug-in hybrid below. The micro-hybrid here mainly refers to a 48V motor and 48V/12V battery, such as the 48V BSG (Belt Starter Generator). The characteristics of its thermal management architecture can be summarized in the following three points.
The motor and battery are mainly air-cooled, but water-cooled and oil-cooled are also available.
If the motor and battery are air-cooled, there is almost no power electronics cooling problem, unless the battery uses a 12V battery and then uses a 12V to 48V bi-directional DC/DC, then this DC/DC may require water-cooled piping depending on the motor start power and brake recovery power design. The air cooling of the battery can be designed in the battery pack air circuit, through the control of the fan way to achieve forced air cooling, this will increase a design task, that is, the design of the air duct and fan selection, if you want to use simulation to analyze the cooling effect of the battery forced air cooling words will be more difficult than liquid-cooled batteries, because the gas flow heat transfer than the liquid flow heat transfer simulation error is greater. If water-cooled and oil-cooled, the thermal management circuit is more similar to that of a pure electric vehicle, except that the heat generation is smaller. And because the micro-hybrid motor does not work at a high frequency, there is generally no continuous high torque output that causes rapid heat generation. There is one exception, in recent years there are also engaged in 48V high power motor, between the light hybrid and plug-in hybrid, the cost is lower than the plug-in hybrid, but the drive capacity is stronger than the micro-hybrid and light hybrid, which also leads to the 48V motor working time and output power becomes larger, so that the thermal management system needs to cooperate with it in time to dissipate heat.
Post time: Apr-20-2023